Injection Molding vs Extrusion: What is the Difference?
Written by
Arterex Medical
Published on
September 6, 2024
Read time
15 minute read
What is Injection Molding?
Injection molding is a manufacturing process where molten material, typically plastic, is forced into a mold cavity under high pressure. The material then cools and solidifies, taking the shape of the mold to produce a wide variety of parts and products.
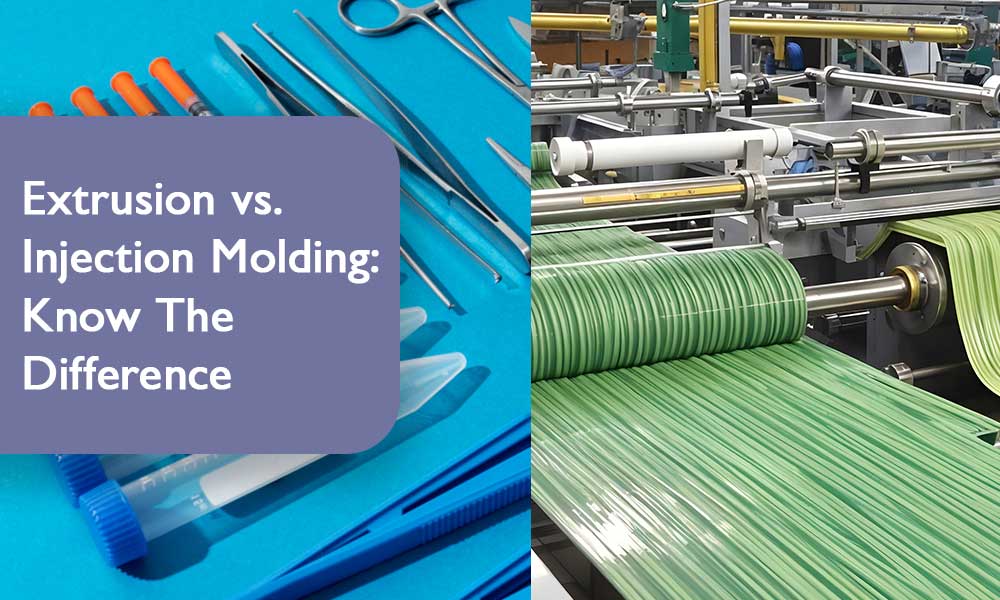
Injection Molding Process
The injection molding process involves the following steps:
1.Material Loading: Plastic pellets or granules are fed into the machine’s hopper.
2.Melting: The granules are compressed in the feed section, where frictional heat melts them into a thick liquid (melt).
3.Injection: The melt is transferred to an injector (which can be screw-driven, piston-driven, manual, or hydraulic) and then forcefully injected into the closed mold cavity.
4.Cooling and Solidification: The molten plastic expands to fill the mold, then cools and solidifies, taking the shape of the cavity.
5.Ejection: Once cooled, the mold opens and ejector pins push out the finished part.
Types of Injection Molding
There are many different injection molding process variations, including:
- Cube molding
- Die casting
- Gas-assisted injection molding
- Liquid silicone rubber injection molding
- Metal injection molding
- Micro injection molding
- Reaction injection molding
- Thin-wall injection molding
Advantages of Injection Molding
Advantages of Injection Molding are listed below:
1.Scalability and Cost-Effectiveness
- Ideal for large-scale production
- Initial costs (design and mold creation) are high, but per-unit costs decrease significantly as production volume increases
- Becomes very cost-effective for high-volume manufacturing
2.Material Efficiency
- Produces minimal waste compared to subtractive manufacturing methods like CNC machining
- Some waste is generated (sprues, runners, gates, and flash), but it’s relatively minimal
- Excess material can often be recycled and reused in the process
3.Consistency and Reliability
- Produces highly identical parts in large quantities
- Ensures part reliability and consistency in high-volume production
- Ideal for applications requiring precise, repeatable results
4.Design Flexibility
- Allows for complex geometries and intricate details
- Can produce parts with a wide range of sizes and shapes
5.Material Versatility
- Compatible with a wide range of thermoplastics and some thermosets
- Can use filled materials for enhanced properties (e.g., glass-filled polymers for increased strength)
6.High Production Rates
- Once set up, can produce parts very quickly
- Automated process requires minimal human intervention during production
7.Surface Finish
- Can produce parts with excellent surface finishes, often requiring little to no post-processing
8.Integration of Features
- Allows for the integration of multiple features into a single part
- Can reduce the need for assembly of multiple components
9.Low Labor Costs
- Highly automated process reduces labor requirements for large production runs
10.Reduced Post-Production Processing
- Parts often come out of the mold in their final or near-final state
- Minimizes the need for additional finishing or machining operations
Limitations of Injection Molding
Limitations of Injection Molding are listed below:
- High Initial Costs
- Significant upfront investment required for mold design and fabrication
- Cost-effective only for high-volume production; not economical for small runs
- Mold modifications can be expensive, making design changes costly
- Material Restrictions
- Primarily limited to thermoplastics and some thermosets
- Limited metal production capabilities (though metal injection molding exists)
- Not suitable for all types of materials or composites
- Design Constraints
- Parts must be designed with uniform wall thickness and appropriate draft angles
- Complex geometries may require multi-part molds, increasing costs
- Limitations on undercuts and certain feature types
- Long Lead Times for New Products
- Mold design and fabrication can take weeks or months
- Not ideal for rapid prototyping or small batch production
- 3D printing may be faster for producing prototype parts
- Large Equipment Requirements
- Injection molding machines are large and require significant floor space
- High energy consumption during operation
- Environmental Concerns
- High power consumption contributes to environmental impact
- Primarily used for plastics, which can have environmental implications if not properly recycled
- Waste generated from runners, sprues, and rejected parts
- Quality Issues
- Potential for defects such as sink marks, warping, and flash
- Consistency can be affected by variations in material, temperature, and pressure
- Limited Flexibility
- Changing production runs or product designs requires new or modified molds
- Not suitable for frequent design iterations or customization
- Material Waste
- While more efficient than some processes, still produces waste from sprues, runners, and rejected parts
- Color Limitations
- Changing colors can be time-consuming and may result in material waste
- Not ideal for small batches of different colors
- Processing Time Considerations
- While efficient for high-volume production, it may not be the fastest option for small batches or prototypes
- Setup time can be significant, especially when changing molds or materials
Common Applications of Injection Molding
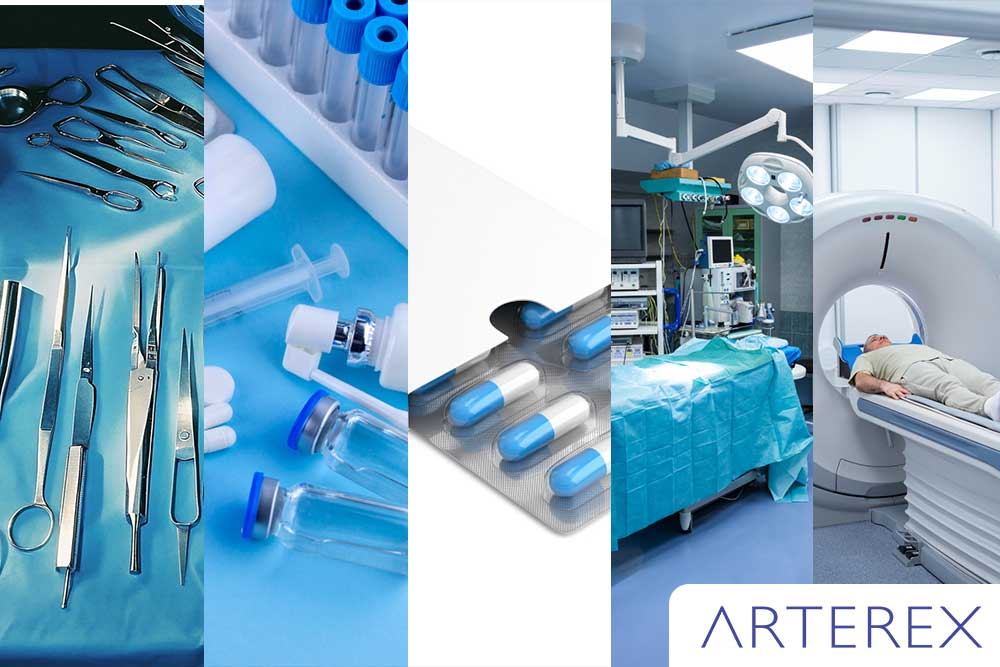
Here’s a comprehensive list of plastic injection molding applications across various industries:
1.Automotive Industry:
- Interior components (dashboards, door panels, consoles)
- Exterior parts (bumpers, grilles, mirror housings)
- Under-hood components (reservoirs, air intake manifolds)
- Electrical connectors and housings
- Fuel system components
2.Medical Industry:
- Surgical instruments and preparation products
- Diagnostic and testing equipment
- Drug delivery devices
- Implants and prosthetics
- Medical packaging
- Personal protective equipment (PPE)
- Hospital furniture and equipment components
- Fluid management systems
- Imaging equipment components
- Bioprocessing and laboratory equipment
3.Consumer Goods:
- Household items (containers, utensils, storage bins)
- Electronics casings (phones, laptops, remote controls)
- Toys and gaming accessories
- Personal care product containers
- Sporting goods (protective gear, equipment components)
4.Packaging:
- Food and beverage containers
- Caps and closures
- Industrial packaging
- Cosmetic packaging
- Pharmaceutical packaging
5.Construction and Building:
- Plumbing fittings and fixtures
- Electrical components (switch plates, outlet covers)
- Hardware and fasteners
- Pipe fittings and connectors
- Insulation components
- Window and door components
What is Extrusion?
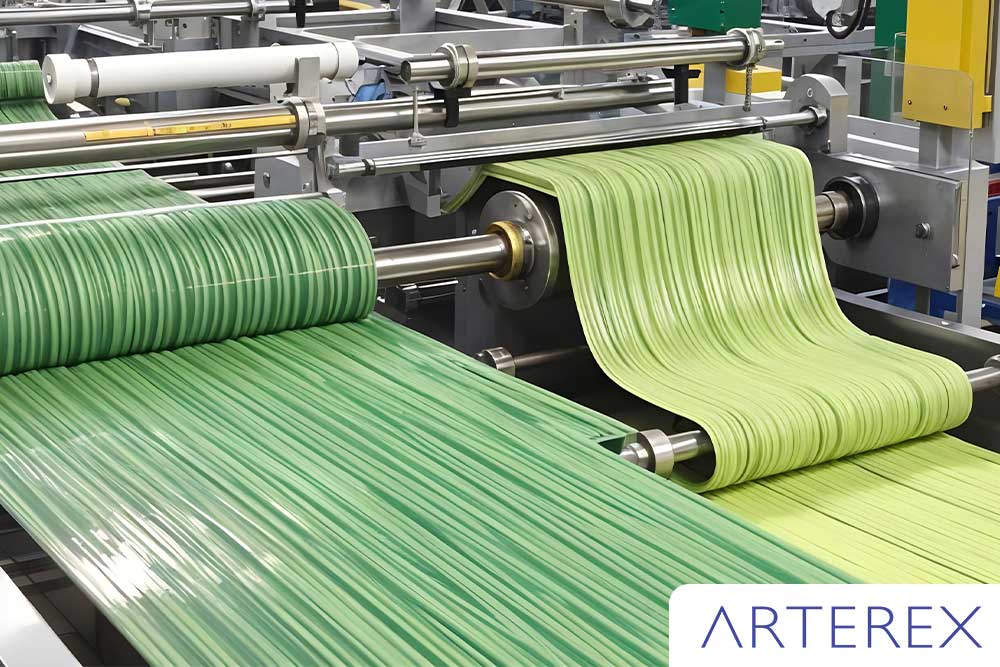
Extrusion is a manufacturing process that involves forcing molten or semi-molten material through a die with a specific cross-sectional profile to create a continuous length of product with a consistent shape. This process was invented by Thomas Hancock in 1820 and was fully established as an industrial manufacturing method by 1935.
Extrusion Process
The extrusion process involves several key steps to transform raw materials into a continuous product with a consistent cross-sectional profile. Here’s a detailed breakdown of the process:
- Material Feeding:
- Plastic granules or powder are fed into the extruder through a hopper.
- The feed material is typically in a solid state at this point.
- Conveying and Heating:
- The material travels through a barrel containing a rotating screw.
- The screw has a specific thread pattern designed for even distribution and mixing.
- Heat jackets or heating elements on the barrel’s exterior gradually melt the plastic.
- The rotating screw action also generates frictional heat, contributing to the melting process.
- Melting and Pressurization:
- As the material moves along the barrel, it transforms into a thick, consistent liquid.
- The screw’s design creates pressure, forcing the molten material towards the die.
- Die Extrusion:
- At the end of the barrel, a die is attached with a shaped opening.
- The die’s cavity determines the cross-sectional profile of the extruded product.
- The molten plastic is forced through this die under high pressure.
- Shaping and Cooling:
- As the material exits the die, it begins to cool and solidify.
- The extruded product maintains the shape of the die opening.
- Cooling may be accelerated using water baths, air jets, or other cooling methods.
- Sizing and Shaping (if necessary):
- Some extrusion processes include additional steps to refine the product’s dimensions or shape.
- This might involve pulling the extrudate at a controlled rate or using shaping tools.
- Cutting or Winding:
- For discrete length products, the extrudate is cut to size.
- For continuous products like tubing or wire coating, the material is wound onto spools.
Types of Extrusion Molding
Extrusion processes can be classified into several categories based on different criteria. Here are the main types:
1.According to the direction of metal flow:
a) Direct Extrusion:
- Metal flows in the same direction as the punch movement.
- The punch moves toward the die during extrusion.
- Higher force required due to increased friction between billet and container.
b) Indirect Extrusion:
- Metal flows in the opposite direction of plunger movement.
- The die is fitted on the opposite side of punch movement.
- Metal flows through an annular space between punch and container.
c) Hydrostatic Extrusion:
- Uses fluid to apply pressure on the billet.
- Eliminates friction as the billet doesn’t contact cylinder wall or plunger.
- A fluid (usually vegetable oil) is placed between billet and plunger.
- Can have issues with leakage and uncontrolled extrusion speed.
2.According to working temperature:
a) Hot Extrusion:
- Process occurs above recrystallization temperature (about 50-60% of melting temperature).
Advantages:
- Lower force required compared to cold working.
- Easier to work with material in hot form.
- Product is free from strain hardening.
Disadvantages:
- Lower surface finish due to scale formation.
- Increased die wear.
- Higher maintenance requirements.
b) Cold Extrusion:
- Process occurs below crystallization temperature or at room temperature.
- Used for products like aluminum cans, cylinders, collapsible tubes.
Advantages:
- Higher mechanical properties in finished product.
- Superior surface finish.
- No oxidation on metal surface.
Disadvantages:
- Higher force required.
- Product experiences strain hardening.
These classifications highlight the versatility of extrusion processes, allowing manufacturers to choose the most suitable method based on the material properties, desired product characteristics, and production requirements.
Advantages of Extrusion
1.Material Versatility:
Extrusion can process a wide range of materials, making it an extremely versatile manufacturing method.
For metals:
- Aluminum is the most commonly extruded metal, accounting for about 80% of all metal extrusions.
- Other metals include copper, brass, steel, titanium, and various alloys.
- Each metal offers unique properties, such as aluminum’s lightweight nature and corrosion resistance, or steel’s strength and durability.
For plastics:
- Polypropylene is the most common plastic for extrusion.
- Other plastics include PVC, polyethylene, polystyrene, and various engineering plastics.
- Thermoplastics are particularly well-suited for extrusion due to their ability to be repeatedly melted and solidified.
This versatility allows manufacturers to choose the most suitable material for their specific application, whether it’s for structural components, consumer goods, or specialized industrial parts.
2.Multiple Processing Methods:
Extrusion offers several processing methods, each with its own advantages:
Hot Extrusion:
- Performed above the material’s recrystallization temperature.
- Requires less force than cold extrusion.
- Ideal for materials that are difficult to work with at room temperature.
- Allows for more complex shapes and larger cross-sections.
Cold Extrusion:
- Performed at or near room temperature.
- Produces parts with better surface finish and tighter tolerances.
- Improves mechanical properties through work hardening.
- Suitable for materials that oxidize easily at high temperatures.
Friction Extrusion:
- Uses friction to generate heat and plasticize the material.
- Can process materials that are difficult to extrude using conventional methods.
- Offers unique microstructural benefits in some materials.
The availability of these different methods allows manufacturers to choose the most appropriate process based on the material properties, desired product characteristics, and production requirements.
3.Cost-Effectiveness:
Extrusion is often more economical than other manufacturing processes, especially for large-scale production:
- Lower tooling costs: Dies for extrusion are generally less expensive than molds for injection molding or tooling for CNC machining.
- High production rates: Continuous production allows for large volumes to be produced quickly.
- Material efficiency: Minimal waste compared to subtractive manufacturing methods.
- Energy efficiency: Generally requires less energy than processes like casting or forging for certain materials.
- Reduced secondary operations: Many features can be incorporated directly into the extruded profile, reducing the need for additional machining or assembly.
For metal parts in particular, extrusion is significantly more cost-effective than CNC machining when producing at scale. This makes it an attractive option for industries requiring large quantities of parts with consistent cross-sections.
Limitations of Extrusion
Disadvantages of Extrusion:
1.Limited Geometric Complexity:
- Extrusion primarily produces parts with constant cross-sections.
- Cannot achieve the intricate 3D shapes possible with plastic injection molding.
- While clamping units can create some complex cross-sections, they’re still limited compared to injection molding capabilities.
- This constraint restricts the range of products that can be manufactured via extrusion.
- Fewer use-cases for extrusion compared to plastic injection molding due to shape limitations.
2.Environmental Concerns:
- Extrusion of metals and plastics can have a significant environmental impact.
- High energy consumption, particularly in hot extrusion processes.
- Potential for emissions and waste products if not properly managed.
- However, the industry is actively working to mitigate these issues:
- Developing more energy-efficient equipment
- Increasing use of recycled materials
- Implementing improved waste management and recycling programs
- Ongoing efforts aim to reduce the overall environmental cost of the extrusion process.
3.Limited Material Options:
- Extrusion offers fewer material choices compared to other manufacturing methods, especially injection molding.
- Not all plastics or metals are suitable for extrusion due to their flow characteristics or thermal properties.
- Some high-performance or specialty materials may be difficult or impossible to extrude.
- This limitation can restrict design options and material selection for certain applications.
- The narrower range of materials may impact the versatility of extrusion in some industries or for specific product requirements.
Common Applications of Extrusion
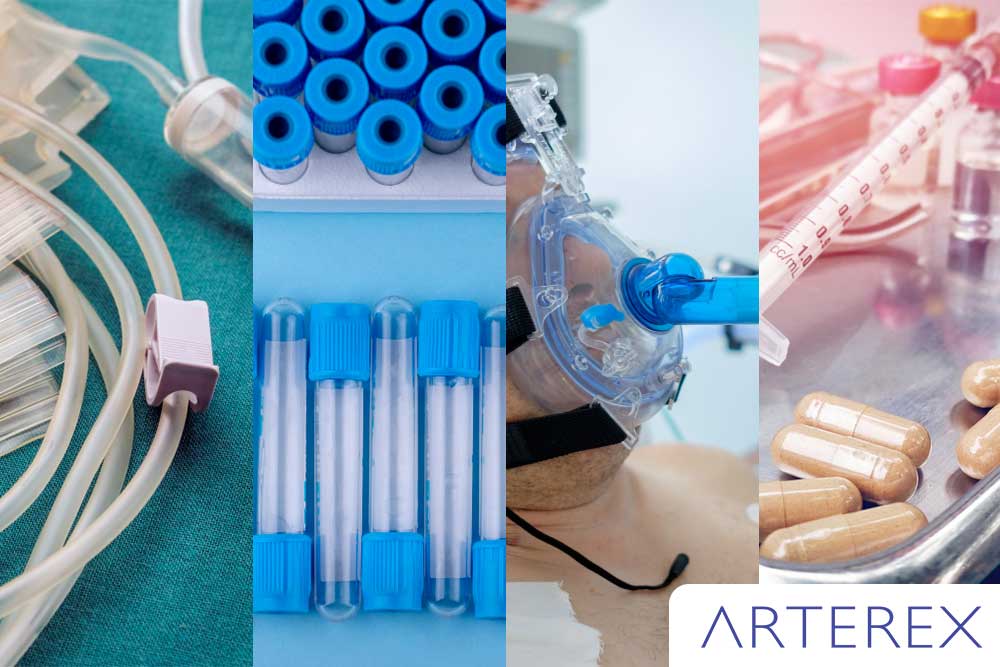
1.Plastic Products
- Pipes and Tubing: Commonly used for PVC pipes, plumbing, and irrigation systems.
- Profiles: Such as window frames, weather stripping, and cable insulation.
- Plastic Films and Sheets: Used in packaging, construction, and various consumer products.
2.Medical Devices
- Catheters and Tubing: Used in various medical applications, including IV lines and respiratory equipment.
- Drug Delivery Systems: Extrusion is used to create controlled-release drug delivery devices.
3.Packaging Industry
- Plastic Bottles and Containers: Extrusion blow molding is used to create hollow plastic bottles and containers for beverages, chemicals, and personal care products.
- Flexible Packaging: Extruded films are used for packaging food, medical supplies, and industrial goods.
4.Rubber Products
- Tire Treads: Extrusion is used to produce the rubber components of tires.
- Seals and Gaskets: Custom-shaped rubber seals for automotive, aerospace, and industrial applications.
What is The Difference Between Extrusion and Injection Molding?
The Difference between extrusion and injection molding are shown in below table:
Feature | Extrusion Molding | Injection Molding |
---|---|---|
Process | Material is continuously forced through a shaped die to create a continuous product with a fixed cross-section. | Material is injected into a mold cavity to create discrete, individual parts. |
Material Flow | Continuous flow of material. | Intermittent, cyclical flow of material |
Product Shape | Creates long, continuous products like pipes, tubes, sheets, or profiles. | Produces discrete, complex parts with high precision, such as plastic components. |
Applications | Used for products like pipes, tubing, window frames, plastic sheets, etc. | Used for products like plastic bottles, automotive parts, toys, medical devices, etc. |
Tooling (Die vs Mold) | Simpler die, as it only defines the cross-sectional shape of the product. | Complex molds with multiple cavities, designed to form the entire product. |
Production Volume | High-volume production of continuous products. | High-volume production of individual, precise parts. |
Cycle Time | Continuous process with no distinct cycle. | Cyclical process with defined injection, cooling, and ejection phases. |
Product Complexity | Limited to simple profiles with consistent cross-sections. | Capable of producing highly complex, intricate shapes with detailed features. |
Material Types | Commonly used for plastics, rubber, metals, and food. | Primarily used for thermoplastics, but also used for thermosetting plastics, metals, and ceramics. |
Tolerances | Generally lower precision and higher tolerances. | High precision and tight tolerances can be achieved. |
Post-Processing | May require additional cutting or shaping after extrusion. | Minimal post-processing; parts often come out of the mold ready for use. |
Cost Efficiency | Lower tooling costs and high efficiency for continuous products. | Higher tooling costs, but efficient for mass production of complex parts. |
Example Products | Plastic pipes, vinyl siding, food products (e.g., pasta). | Plastic toys, bottle caps, automotive components, medical devices. |
- What is Injection Molding?
- Injection Molding Process
- Advantages of Injection Molding
- Limitations of Injection Molding
- Common Applications of Injection Molding
- What is Extrusion?
- Extrusion Process
- Advantages of Extrusion
- Limitations of Extrusion
- Common Applications of Extrusion
- What is The Difference Between Extrusion and Injection Molding?