Challenges and Risks in Medical Device Contract Manufacturing
Written by
Arterex Medical
Published on
July 26, 2024
Read time
8 minute read
Medical device contract manufacturing comes with several challenges and risks that both the device company and the contract manufacturer need to navigate carefully. Understanding these challenges and risks can help in developing strategies to mitigate them. Here are some of the key challenges and risks
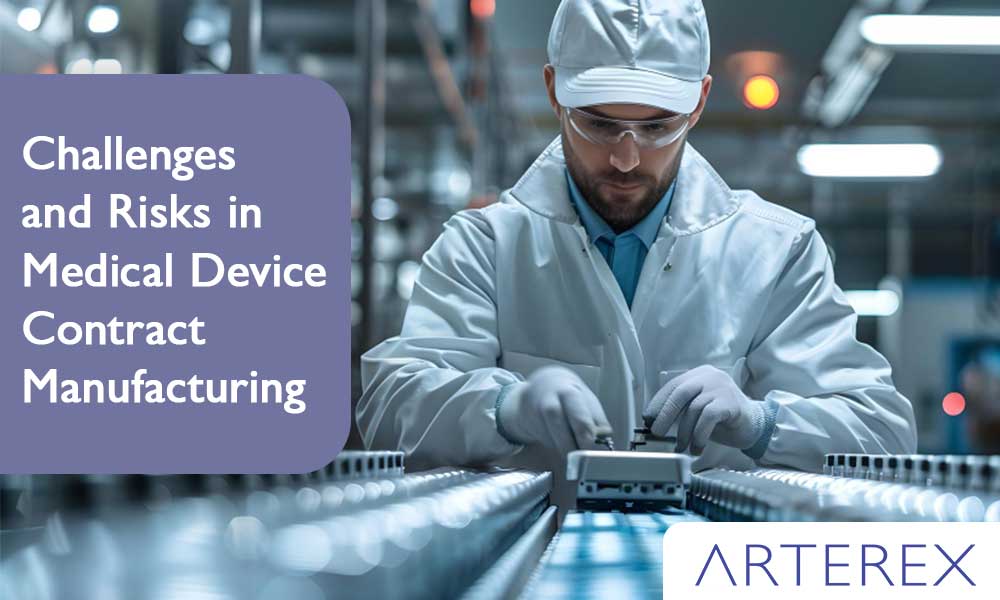
1. Regulatory Compliance
- Complex Regulations: Navigating the complex and evolving regulatory landscape can be challenging. Ensuring compliance with FDA, ISO, EU MDR and other international standards requires meticulous attention to detail and ongoing monitoring.
- Regulatory Changes: Changes in regulatory requirements can impact production processes and product design, necessitating quick adaptation to maintain compliance.
2. Quality Control
- Consistency: Maintaining consistent quality across all lots can be difficult, especially for complex devices. Variation can lead to product failures or recalls.
- Process Validation: Ensuring that all manufacturing processes are properly validated to produce reliable and safe products is critical but can be resource-intensive.
3. Communication and Coordination
- Miscommunication: Poor communication between the device company and the contract manufacturer can lead to misunderstandings, errors, and delays.
- Coordination: Coordinating activities, especially across different geographic locations or time zones, can be challenging and requires robust project management.
4. Intellectual Property (IP) Protection
- IP Theft: There is always a risk of intellectual property theft or misuse when sharing proprietary information with a third-party manufacturer.
- Confidentiality: Ensuring that the contract manufacturer adheres to strict confidentiality agreements to protect sensitive information is crucial.
5. Supply Chain Management
- Material Shortages: Disruptions in the supply chain, such as material shortages or delays, can impact production schedules and delivery timelines.
- Supplier Reliability: The reliability and quality of suppliers can affect the overall quality and consistency of the final product.
6. Cost Management
- Hidden Costs: There may be hidden costs or unexpected expenses that arise during the manufacturing process, impacting the overall project budget.
- Cost Overruns: Managing costs effectively to avoid overruns while maintaining quality and compliance can be challenging.
7. Technological Compatibility
- Integration Issues: Ensuring that the contract manufacturer’s technology and processes are compatible with the product’s requirements can be complex.
- Keeping Up with Innovation: Rapid advancements in manufacturing technologies may require continuous investment and adaptation, which can be a challenge for both parties.
8. Product Delays
- Production Delays: Delays in the production process due to equipment failures, quality issues, or other unforeseen events can impact time-to-market.
- Regulatory Delays: Delays in obtaining regulatory approvals can also impact the production timeline and market entry.
9. Geopolitical and Economic Risks
- Trade Policies: Changes in trade policies, tariffs, and regulations in different countries can affect the cost and logistics of manufacturing.
- Economic Instability: Economic instability in the region where the contract manufacturer operates can impact production and supply chain stability.
10. Cultural and Language Differences
- Cultural Barriers: Differences in business culture and practices can lead to misunderstandings and misalignments between the device company and the contract manufacturer.
- Language Barriers: Language differences can complicate communication and documentation, potentially leading to errors.
11. Scalability Issues
- Production Scale-Up: Scaling up production from prototyping to full-scale manufacturing can present challenges in maintaining quality and consistency.
- Capacity Limits: The contract manufacturer’s production capacity may be limited, affecting their ability to meet increasing demand.
12. Legal and Contractual Issues
- Disputes: Legal disputes can arise over contractual terms, IP rights, quality issues, and other aspects of the partnership.
- Contract Enforcement: Ensuring that the contract terms are enforceable and adhered to by both parties is critical for a successful partnership.
Top Medical Device Contract Manufacturers
When selecting a medical device contract manufacturer, it’s important to consider those with a proven track record of quality, regulatory compliance, and innovation.
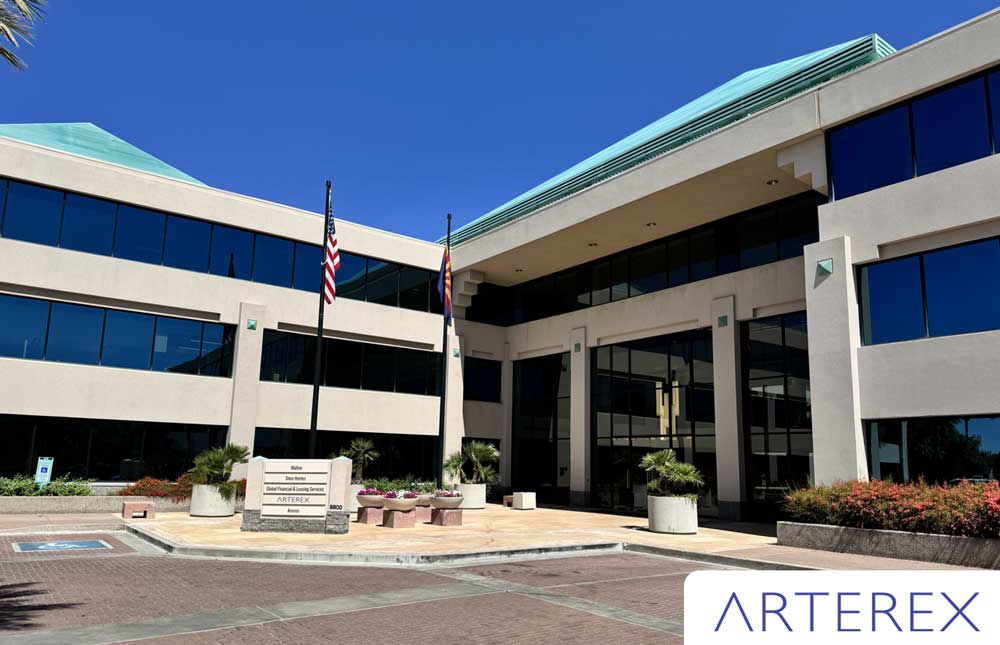
Here are some of the top medical device contract manufacturers, with Arterex Medical highlighted as a leading player in the industry:
- Overview: Arterex offers comprehensive, integrated contract manufacturing services for components to Class II and III therapeutic and diagnostic medical devices. We ensure quality, speed, and smooth market transitions with our extensive manufacturing capabilities and engineering expertise.
- Key Features: ISO 13485:2016 certified, FDA registered, cGMP compliant, ISO Class 7 & 8 clean rooms, LEAN manufacturing culture, and facilities in North America, Europe, and North Africa. Services include medical device design & development, high precision injection molding, micro molding, electromechanical assembly, and full end-to-end supply chain management.
SeaskyMedical
- Overview: SeaskyMedical specializes in high-grade medical molding solutions, offering comprehensive support across all phases of the assignment, including product design, mold manufacturing, material selection, and plastic injection molding.
- Key Features: ISO 13485 certification, Class 7 clean room, and advanced medical molding technologies ensure quality and sterilization of medical device parts.
Scapa Healthcare
- Overview: Scapa Healthcare is a strategic partner for medical device component manufacturers known for their expertise in wound care and consumer wellness. They leverage high-end technology and development expertise to create innovative solutions.
Spectrum Solutions
- Overview: Spectrum Solutions provides a full range of services, from product development and prototyping to manufacturing and packaging. They are ISO 13485 certified and FDA registered.
HDA Technology
- Overview: HDA Technology excels in designing and manufacturing medical devices and components. They offer end-to-end services, from engineering and prototyping to assembly and packaging, helping clients bring products to market efficiently.
Market Size of Medical Device Contract Manufacturing
As of 2024, the global medical device contract manufacturing market was valued at approximately $78.9 billion.
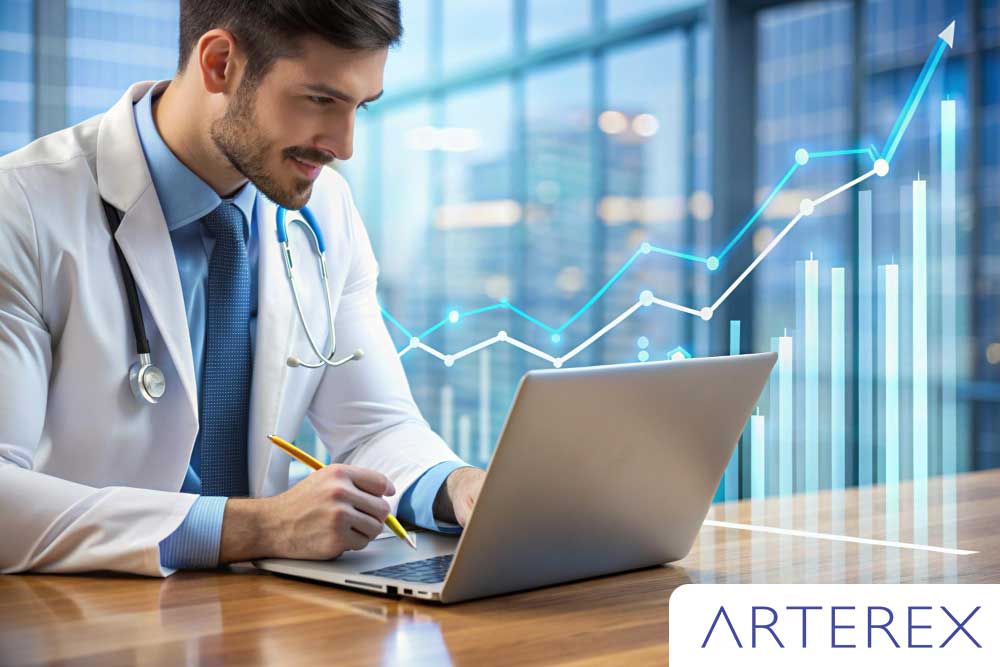
It is expected to grow at a compound annual growth rate (CAGR) of around 11.4%, reaching $149.4 billion by 2029, reflecting robust demand and ongoing industry expansion.
Why Choose Arterex for Contract Manufacturing?
Choosing Arterex as your contract manufacturing partner offers numerous advantages, ensuring high-quality, efficient, and compliant production of medical devices. Here’s why Arterex stands out:
1. Comprehensive Services
Arterex provides a full range of integrated services from initial concept development to product design & development full-scale production and distribution. Our capabilities cover everything from components to Class II and III therapeutic and diagnostic medical devices.
2. Regulatory Compliance
Arterex is ISO 13485:2016 certified, FDA registered, and cGMP compliant, ensuring that all products meet the highest standards of quality and safety. They also operate ISO Class 7 & 8 clean rooms, which are essential for maintaining sterile environments.
3. Advanced Manufacturing Capabilities
Arterex utilizes cutting-edge technology, including high precision injection molding, micro molding, and complex disposable device manufacturing. Our facilities are equipped with 110 molding machines (some more at Luc & Bel with presses and square footage devoted to molding) and a 240,000 sq. ft. campus, allowing for high cavitation and tight tolerance production.
4. LEAN Manufacturing Culture
Arterex’s commitment to LEAN manufacturing principles fosters a culture of continuous improvement. This approach ensures ongoing enhancements in product quality and cost reduction, providing efficient and effective manufacturing solutions.
5. Global Reach
With manufacturing facilities in North America, Europe, and North Africa, Arterex can serve clients worldwide. This global presence enables them to manage supply chains effectively and deliver products across multiple geographies.
6. Expertise and Experience
Arterex’s team brings extensive experience and technical expertise to every project. Our engineering and manufacturing capabilities ensure that even the most complex projects are handled with precision and care.
7. Supply Chain Management:
Arterex manages the entire supply chain, from sourcing raw materials to managing inventory and logistics. Our efficient supply chain operations ensure timely and cost-effective procurement and delivery of materials and finished products.
8. Post-Production Support:
Arterex offers comprehensive post-production support, including customer service, maintenance, and product updates. They use market feedback to continuously improve Our products and processes.
9. Material and Process Expertise:
Arterex excels in various materials joining techniques, such as laser beam welding, resistance welding, TIG welding, ultrasonic welding, and adhesive bonding. They also perform rigorous performance testing, including leak and flow, pressure, continuity, and biocompatibility tests.
10. Flexibility and Scalability:
Arterex’s scalable manufacturing capabilities allow them to handle both small-scale prototypes and large-scale production runs, adapting to the changing needs of our clients.